By Kerri Jansen STAFF REPORTER Published: November 19, 2014 12:04 pm ET Updated: November 19, 2014 1:30 pm ET
Image By: Photo collage by Jessica Jordan
As Plastics News staff was putting together this special issue, someone floated the idea to include then-and-now photos showing staff in ’89 and today. We could marvel over youthful faces, chuckle over questionable fashion choices … and wonder where Kerri was, because it’s hard to get a photo of someone who hasn’t yet been born.
At 25, Plastics News is older than I am. And for this anniversary issue, I sought out members of my own millennial generation, who like me grew up as Plastics News did and are now entering the plastics industry ready to carry it forward over the next 25 years.
We talked about what drives them, what challenges them and what they see in the future.
Here’s what they had to say.
Responses have been edited for brevity and clarity.
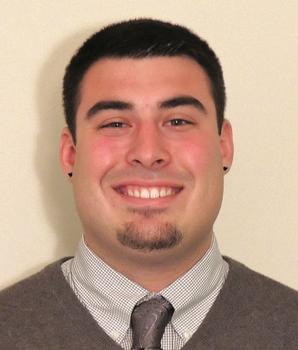
Matthew Peterman
Matthew Peterman, 21
Senior at Pennsylvania College of Technology, Plastics and Polymer Engineering Technology
Matthew has held internships at Rodon Group LLC and East Penn Manufacturing Co. Inc. He is currently president of his college’s student chapter of the Society of Plastics Engineers and part of SPE’s Next Generation Advisory Board.
Q: Why plastics?
Peterman: My senior year in high school I had an engineering materials course and we focused really heavily on a really big chunk of plastics processing. All lab-scale demonstrations and stuff, but it was really catching to me, and that’s how I started to look into plastics.
Q: What’s an accomplishment you’re proud of?
Peterman: I think I worked for some really good companies in my past summers. Just coming out of school as a first-year student and landing a pretty good job with the Rodon Group my first summer I felt was a pretty good accomplishment.
Q: What are some challenges you have faced?
Peterman: I think finding a way to connected is a good challenge. I utilized [SPE] to kind of break that challenge of getting connected and networking in a group, but I think overall my generation in this field struggles to get connected and network with the existing professionals in the industry.
Q: How would you like to have an impact on the industry?
Peterman: I want to be a leader in the industry. I’m very involved with SPE, I’m involved with their Next Generation Advisory Board, so my goal is that I’d like to become more involved with the national SPE chapter, become involved with the SPE in whatever area I work in the United States, and continue spreading the knowledge of plastics and what the industry is to the next generation below me. And I’d like to work with my college to promote the industry. That’s my goal.
Q: What’s next in your career?
Peterman: I like to problem-solve so I’m looking toward process engineering. And I’ve had a lot of internships in injection molding — that’s where the bulk of my summer internships were focused on — so I might be heading toward process engineering in an injection molding company.
Q: What could a company do to make itself stand out to you?
Peterman: A company that really stands out to me is one that looks at more than just my grades are — what I’ve done along with my education, what my background is along with my involvement in the industry. A company that looks at not just the first chunk of my resume that says where I went to school and my grades, but they’re really focused on what I’ve done and what I’ve been involved with.
Q: What do you think is the most exciting thing in the industry right now?
Peterman: We do so many cool things; that’s a hard question. We have a composites course in school, about the advancements in the advanced composite materials; I think that’s really cool.
Just the different ways they’re using carbon fibers and the more advanced fiberglass materials in more than just the old traditional methods. The new carbon fibers are a lot more advanced with different fabric designs, different capabilities. Race cars — that’s completely carbon fiber now. But they’re implementing that into other industries, medical industries, prosthetics, stuff like that. That has become really cool.
Jason Paris
Jason Paris, 25
Process engineer at Ring Container Technologies Corp. in Fontana, Calif.
Jason relocated from Pennsylvania to California after being offered a job at Ring Container, where he has been employed for more than two years. He has a bachelor’s degree in plastics and polymers engineering from Pennsylvania College of Technology.
Q: Why plastics?
Paris: They actually did an information session at Penn College and recruited students from our program.
My uncle went through the Behrend plastics program [at Penn State Erie], so it was kind of in my family and I was kind of given that guidance at a younger age.
Q: What’s an accomplishment you’re proud of?
Paris: For one, being able to relocate to Southern California from Pennsylvania after college to take the position. It’s really a great opportunity for me.
I did have a couple of interviews lined up locally, but they actually flew me out to California to come to the plant during winter break, so I already had an offer on the table for a position before I graduated.
Q: What are some challenges you have faced?
Paris: I think from a young professional’s perspective, the hardest thing is going from college where the possibilities are endless — there are multiple things you can do and multiple companies — and then you get into your niche and go into a specific company, dealing with that. Taking the day-to-day, the discipline, the grind of the job.
But also another challenge is taking all the knowledge that you gained and putting it into practical use. And I think that’s where engineers come in largely, is taking all that knowledge they learned and being able apply it practically, and that was a challenge.
Q: What can companies do to help employees your age find success?
Paris: I think they just need to stay fast-paced in the beginning. They need to keep it exciting, put you in a position where you have an opportunity to prove yourself and go through multiple trainings. One thing is I get to travel, so that really helped make it very interesting and fun. I can go to other facilities within the company and see different technologies, train with multiple people, and that really makes you feel like part of the family, of our company, and I think that’s something that other companies should embrace.
Q: What are your goals for your career?
Paris: Definitely to continue down the engineering path, to go hopefully into a corporate engineering position at some point.
Brittany Caldwell
Brittany Caldwell, 22
Technical sales assistant at Reedy International Corp. in Charlotte, N.C.
Brittany has a bachelor’s degree in chemical engineering from the University of South Carolina. She has been at Reedy International, which is also celebrating its 25th anniversary this year, for five months.
Q: Why plastics?
Caldwell: There was a job opening on LinkedIn, so I contacted the company, and they invited me in.
When I was in high school I always wanted to be in business, and then I had a teacher who convinced me to do chemical engineering. So I saw the opportunities available as a chemical engineer, and I always just saw myself being on the more business side of engineering. My whole idea as a freshman in college to get a chemical engineering degree, and have a degree that can back up my sales skills. And that’s exactly the kind of position I’m in.
Q: What are some challenges you’ve faced?
Caldwell: The majority of the folks who come in as technical sales have either (a) been a part of the same company’s manufacturing department, or (b) they’re a business who have done sales in a technical field. And one thing I’ve struggled with is being able to learn how to use our product within different processes and the fact that I’m new to the industry — not brand new, because I did an internship in the plastics industry — but as far as the longevity of knowing plastics inside and out, I’m still trying to learn that.
There are all these different kinds of plastics applications that I’m still trying to learn and be able to basically be an expert in each of them so I can provide customers with the correct information product-wise. I jumped into every class that I could get into that would teach me anything about injection molding and extrusion. I try to take advantage of webinars that are available, I do a lot of listening with our technical team so when they’re on technical calls, and even whenever I get a chance to go on technical visits and I’m seeing processes and getting to learn different applications.
Q: What are your goals for your career?
Caldwell: I would basically like to be a part of a company’s growth in general, bring the technology and analytical stuff I learned from college and bring it more into the current field of plastics.
You go from college where you’re learning all these different cool math programs that spit formulas out at you, and then you get into the industry and you’re still using Excel. In college, we’re really not taught much about Excel because there’s technologies that are above Excel that are almost more beneficial to processes. So I’d like to bring more technology and just new ideas to the plastics industry and new ways to go about using plastics, using additives, using anything that I can basically think of.
A lot of people in the plastics industry have been here a while, so bringing a new face, new changes, new ideas, I think will help bring a lot of new innovation to the world of plastics.
Q: What makes a company stand out to you?
Caldwell: Growth and opportunity is the main thing. And especially as a new graduate, that’s the No. 1 thing on the list, is you’re always looking for the opportunity to grow and develop within a company. And when you’re given a voice and are able to have it be heard, it brings a lot of opportunity for new innovation. I think new innovation within companies is what keeps them from faltering and keeps them moving forward with purpose.
Q: What do you think is the most exciting thing in the industry right now?
Caldwell: Innovation is exciting. The exposure of 3-D printing. There’s so many different new aspects to plastics that are going around. And technology is starting to rapidly increase, and just seeing technology increase I feel means a lot of innovation and a lot of cool things are due for us in the future.
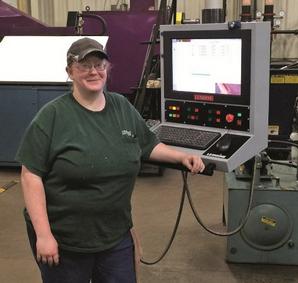
Danyel Dutcher
Danyel Dutcher, 25
Gun drill operator at Franchino Mold & Engineering Co. in Lansing, Mich.
Danyel started at Franchino two years ago as a shop helper. Her father has been with the same company for more than 30 years.
Q: Why plastics?
Dutcher: I needed a job, and they needed someone to sweep their floors. Now I run a gun drill.
I moved around a little bit after high school, I worked at horse barns. This is the first actual job I’ve ever had. I worked at a barn for a while, then I got out of that and moved to California briefly to work at my friend’s family’s farm. I’m not a California girl so I moved back, and now I’m here. I needed a job and Dad worked here and he got me an application.
What are some challenges you have faced?
Dunbar: I like my guys. They’re kind of my family. It was more interesting being the only girl, up until a few weeks ago [when Franchino hired Liz Parish]. It was just a very different environment for me, because everybody is all technical about stuff, and I’m like, ‘You know the thing that does the one thing that spins around like that?’ That’s how everything makes sense to me. When Liz showed up I said something like that and she got it. So there’s that whole how guys see things and how girls see things differently.
I think it was more shell shock for them than it was for me. Everybody was all scared of offending me for a long time and I said, ‘Guys, just be you and I’ll be me and everything will be fine.’
What are your plans for the future?
Dunbar: I don’t really want to go to college, but I need to go to college if I’m ever going to do what I really want to do. So I’m trying to reconcile those things.
I did a couple college classes right out of high school, but just the whole way my school worked was a lot different than how anything else works, so I feel really awkward in a school setting. In my school you kind of just picked your own pace and as long as you got done what you needed to get done by the time you could basically do it however you wanted. There was no teacher at the front of the classroom, you read about it and you looked at the examples and you just did it. And so that’s how I learned to do things. I can’t listen to somebody drone on and on in a lecture; I’m very hands-on.
At Franchino my team leader just shows me what to do, tells me how to do it, and if I have questions he’ll answer them. That works a lot better for me than other training programs.
Keegan Rasmussen, left, and Danny Dunbar
Keegan Rasmussen, 25
CNC machinist at Eifel Mold & Engineering in Fraser, Mich.
Keegan, a military veteran, has worked at Eifel for nine months and is taking classes Oakland Community College, working toward his welding certificate and machinist’s certification.
Q: Why plastics?
Rasmussen: I had gotten out of the Army and hadn’t really been doing anything, kind of struggling to find what I wanted to do with myself. I was just doing random handyman jobs, working with my hands; I like doing that kind of stuff.
After I heard about the opening at Eifel, I came in, talked to [CEO] Rick [Hecker], talked to the shop manager. They walked me through everything, and I kind of just fell in love with it. The atmosphere, working here and being able to work with my hands tangibly every day is just a great thing.
Q: What’s an accomplishment or career highlight?
Rasmussen: There’s actually been quite a few things. Rick’s a great boss; since he’s hired me it’s been one thing after another that have been really great. [My coworker] Danny [Dunbar’s] mom actually donated her old tools — she used to work at Ford — they gave me her old tool set so I had stuff to use while I was here. So that was really huge, but I just like the industry. I like American manufacturing. I like being able to give back to my country any way I can.
Q: What are some challenges you have faced?
Rasmussen: The one thing I immediately came to realize is you could do this job for 20 years and you’ll never know everything, because it’s constantly evolving, new stuff just as fast as you’re learning the current stuff. So that’s a pretty big personal hurdle. It’s a lot to wrap your head around.
I think it’s been hammered into people that you need to go and be a doctor, you need to go and be this top tier thing. People have forgotten about American manufacturing and how that kind of built this country. I think that’s being bred out of modern society, that jobs like these are important.
Q: What are your goals for your career?
Rasmussen: I’d like to work here for absolutely as long as possible, and see how far I can go here. I wouldn’t mind owning a shop, operating a shop, being a shop manager, maybe become a little more specialized. I like firearms, so anything like gunsmithing, that’d be cool for me.
Q: How would you like to have an impact on the industry?
Rasmussen: I think it would be just continuing the platform that Rick has been going with here. He’s made it a point to bring in young guys who want to strive to do better. We need to have a platform for American manufacturing to keep on moving forward and keep on growing.
Q: What do you think is the most exciting thing in the industry right now?
Rasmussen: I think the resurgence in the auto industry is really exciting. It kind of took a dive and now it’s coming back and it’s kind of cool to watch it happen first-hand, especially with big-name brands like Tesla trying to make a big North American push. It’s really exciting to be a part of that.
Danny Dunbar, 23
Design engineer at Eifel Mold & Engineering in Fraser, Mich.
Danny has worked at Eifel for two years and is taking engineering classes at Macomb Community College. She has a degree in fine arts from Oakland University.
Q: Why plastics?
Dunbar: I was trying out all sorts of different things and I got an opportunity to come in and try out the design software to see if it would be something that I would be interested in. I ended up teaching myself how to run the program and shortly thereafter [CEO of Eifel] Rick [Hecker] gave me a job and has been helping me go to college for an actual engineering degree.
I have a pretty well-rounded set of skills as far as employment goes. I’ve done everything from construction to painting murals and more art-based stuff. Rick was looking for somebody who had more of an artistic sense because he’s looking to get into product design over here, so that’s where I came in.
Q: What’s an accomplishment you’re proud of?
Dunbar: Partly the network that I’m getting to know here and the actual skills that it’s taking to reverse engineer a process into molds, I think that’s a pretty good skill to have.
Q: What are some challenges you have faced?
Dunbar: It would be companies taking the step to train younger people. There’s a big disconnect between what they teach in the colleges and what you actually need knowledge-wise in the industry. In the colleges they teach you what all the buttons do, but they don’t teach you how they apply to what it is you’re actually making. It’s really up to the companies to hire on people who don’t know anything and teach them that, but it seems like they don’t really want to do that.
Q: What are your goals for your career?
Dunbar: I do plan to stay at Eifel. I thoroughly enjoy doing what I do; it’s mentally challenging. It’s like I get a puzzle every day. And keep doing my art business on the side and hopefully get my engineering degree fairly soon.
Q: How would you like to have an impact on the industry?
Dunbar: It would be nice to see more women in the industry. And people taking a chance with people my age.
Q: What do you think is the most exciting thing in the industry right now?
Dunbar: I would say additive manufacturing, 3-D printing. As far as the industry goes, I see that being the next big step, being able to build these molds out of metal without having to cut and fix and cut and fix.
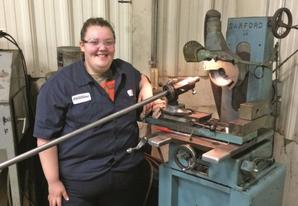
Liz Parish
Liz Parish, 19
Shop helper at Franchino Mold & Engineering Co. in Lansing, Mich.
Liz, a graduate of Portland High School in Portland, Mich., has been at Franchino for about two months and said she hopes to use the company’s educational benefit to take more classes.
Q: Why plastics?
Parish: I took a machining class [at Heartlands Institute of Technology in Ionia, Mich.] when I was in high school for two years, and I actually heard about Franchino through there, so I decided that I was going to make it a job, make it a career.
Being able to work on a machine and take something that was just a plain old square and turn it into something that is functional and can actually be used for another job or to help somebody was something that I thought sounded really cool.
Q: What are some challenges you have faced?
Parish: I feel like a lot of times the people that have been here for years and years, some of them are very set in their ways, so sometimes that’s a challenge. You come in with a different understanding of something and they might not see it the same way you do, so it’s always kind of a challenge trying to merge your two views.
I haven’t gotten into too much of that yet, but I’ve definitely heard of people butting heads a little bit with the younger kids. When I started I hadn’t driven a fork truck, so I was slow and I took a long time on them, but they’ve aided me along quite a bit.
Q: What are your goals for your career?
Parish: I would like to be one of the people running the big machinery, so I can work on these multimillion-dollar machines, and learn how to make them do backflips. To be one of the people making the big parts and doing the jobs that help get all the big products out the door.
My ultimate goal is to be able to manufacture artificial limbs. When I was in seventh grade, my grandpa lost his leg. Just watching the struggles that he went through. Then after I started the classes at Heartlands, now I really see how people can do this and how you can make artificial limbs and joints and things like that. And it’s a cause that’s close to my heart, and so once I started dabbling in the machining and mold process I was could really see it happening. I would like to maybe end up someplace or find out more about how to manufacture artificial limbs.
Q: What’s an accomplishment you’re proud of?
Parish: There are little things everyday. Moving something with a fork truck — yesterday I had to move a bunch of big angle blocks, and they were really kind of rickety on the fork trucks so I had to have somebody help me, but then I was moving a bunch of things on my own. Fork trucks have always made me nervous and I have to move big objects. So I’m getting better, so it makes me feel a little better when I can do the task in half the time it normally takes me.
Q: What can companies do to help employees your age find success?
Parish: Be open to new ideas. Make sure that just because it’s the stereotypical young person, you don’t think they’re not going to know anything. Obviously we don’t know everything because we don’t have the experience behind us, but we wouldn’t be here if we didn’t have some knowledge behind us.
Q: What do you think is the most exciting thing in the industry right now?
Parish: It’s been really busy, and that’s definitely an exciting thing, because there are always new products coming in all the time. There’s really never a lack of work to be done, so you’re always busy, which is definitely a good thing.
|